Mespack és un fabricant de solucions d’envasament flexible i final de línia, per la qual cosa dissenya i produeix maquinària per a empreses de béns de consum envasats arreu del món. Nascuda fa 30 anys com una empresa familiar, avui en dia forma part del grup Duravant i és una companyia innovadora que ofereix tecnologies creatives, funcionals i sostenibles d’envasament. Precisament per aquest esperit innovador, va identificar l’oportunitat d’incorporar la tecnologia de fabricació additiva per a diferenciar-se i oferir més valor afegit als seus clients. Hem parlat amb Guillem Clofent, director general a Mespack, perquè ens expliqui quina ha estat la seva experiència dins l’acceleradora i quins aprenentatges n’han extret.
Què feu a Mespack?
Som una empresa líder en el sector de les màquines per produir envasos flexibles i finals de línia. Aquestes línies de producció que fabriquem poden arribar a tenir 25 metres de longitud, i en tenim per envasat de producte líquid, pols i sòlid, en formats de sobres, doypacks (sobres que s’aguanten drets) i stick packs (els sobres allargats de sucre, per exemple). També fabriquem unes màquines que serveixen per envasar productes on el material de l’envàs desapareix amb l’ús del producte. Per exemple, pastilles hidrosolubles per rentavaixelles i rentadores o fins i tot productes amb envàs comestible.
Com arribeu a considerar l’ús de fabricació additiva?
Nosaltres treballem i implementem plans estratègics periòdics. Justament en el pla que acaba aquest 2023, hi ha algunes línies que convergeixen de manera molt natural amb la impressió 3D. És el que n’hem dit les 6R, i que ens fa treballar per ajudar a la indústria de l’envàs flexible a adoptar lògiques d’economia circular. I precisament la fabricació additiva pot ajudar en la reducció, no només de l’empremta ecològica, sinó també en la millora de les prestacions i del valor que pots oferir als clients.
“Treballem per ajudar a la indústria del packaging flexible a adoptar lògiques d’economia circular”
Com vau abordar la possible introducció de la impressió 3D en l’organització?
Primer, de la mà de ThinkIn 3D ens vam plantejar un seguit d’objectius a aconseguir amb la implementació de la fabricació additiva. Des d’aconseguir una reducció de costos en la producció, passant per millorar la funcionalitat i prestacions del que fabriquem, reduir els terminis d’entrega i millorar el nivell de servei que oferim als clients. Finalment, també vam incloure un objectiu que hem arribat a comprendre gràcies a treballar de la mà de l’acceleradora, i és que aquesta iniciativa ens ajuda a promocionar i mantenir el talent.
“De la mà de ThinkIn 3D ens vam plantejar un seguit d’objectius a aconseguir amb la implementació de la fabricació additiva”
Com s’han concretat aquests objectius?
Un dels productes que hem fet realitat incorporant la impressió 3D és la fabricació d’un tub molt senzill que ens serveix per recollir el retall sobrant que generen les màquines. Fins ara, fabricàvem aquesta peça a partir de 3 subpeces que, a més a més, s’havien de soldar i portar a pintar. Això sense comptar que cada màquina que fabriquem tenia aquesta peça però adaptada i, per tant, fèiem moltes peces lleugerament diferents que feien la mateixa funció. En aquest marc, era impossible aplicar economies d’escala. Dins l’acceleradora hem redissenyat aquesta peça amb fabricació additiva i hem assolit alguns dels objectius de la nostra llista.
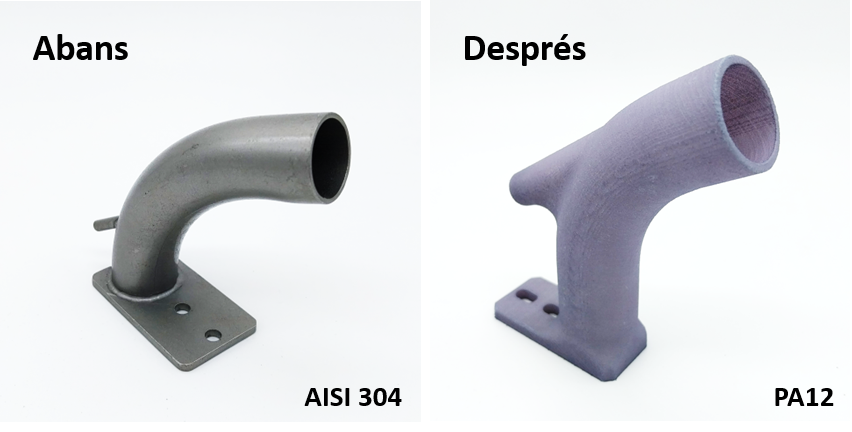
Quins objectius heu aconseguit?
El més clar és una reducció d’un 45% del cost de fabricació. Però també el fet que hem pogut estandarditzar el disseny de la peça per tota la gamma de màquines, de manera que avui som capaços de fabricar una única peça que aplicarem a tota la nostra maquinària. D’altra banda, també hem reduït el temps d’entrega de la peça de tres setmanes a una setmana o menys.
“Hem redissenyat una peça amb fabricació additiva i hem aconseguit una reducció d’un 45% del cost de fabricació”
Heu portat a terme algun altre desafiament d’impressió 3D amb ThinkIn 3D?
Sí. També ens vam plantejar dissenyar amb fabricació additiva un filtre que fem servir per dosificar sabó. El repte de partida és que, quan treballes amb sabó, has de vigilar de no posar molta pressió perquè sinó generes més escuma que líquid dins del sobre. Però, per contra, també ens interessa aplicar pressió perquè el temps necessari per omplir el sobre sigui el més curt possible. Per solventar-ho, fabriquem un filtre amb perforacions capil·lars que eviten la generació de micro escuma. Fabricar aquesta peça avui en dia ens suposa un cost molt elevat perquè és d’acer inoxidable i necessita de moltes hores de mecanització.
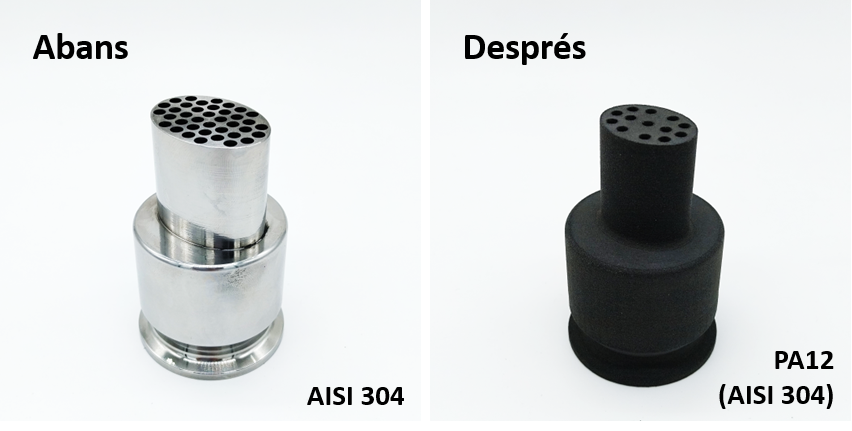
Quin va ser el resultat d’abordar aquest repte amb impressió 3D?
Hem redissenyant la peça amb fabricació additiva, i hem pogut reduir un 75% el cost de producció. Un altre dels avantatges que hem aconseguit és una especialització en el disseny -filtres diferents en funció del producte a dosificar- amb un temps de producció realment ràpid. I, finalment, hem aconseguit que el filtre dissenyat redueixi el temps de dosificat i augmenti la capacitat productiva del client.
“Altres avantatges que hem aconseguit és una especialització en el disseny i un temps de producció realment ràpid gràcies a la impressió 3D”
Quins altres reptes futurs us plantegeu?
Actualment aquest filtre és de poliamida, però l’objectiu és acabar-lo fent d’acer inoxidable per poder-lo fer servir en aplicacions alimentàries com ara els làctics.
Quines lliçons heu après d’aquest procés d’aplicació de la impressió 3D?
En primer lloc, malgrat tots els estalvis en el cost de producció, aquests marges no justifiquen la inversió que hem hagut de fer des del punt de vista de la incorporació de maquinària, la incorporació d’equip i la seva formació. Entenem però que el més important és que ens permet aportar més valor al nostre client, i nosaltres podem capturar part d’aquest valor de diferents maneres: assolint un major marge, per exemple, però també amb un increment de vendes en ser capaços d’oferir peces de recanvi competint amb fabricants locals perquè precisament podem tenir la peça molt mes ràpid que qualsevol altre empresa local que fabriqui per extracció.
“Hem après que la fabricació additiva ens permet aportar més valor al nostre client, i nosaltres podem capturar part d’aquest valor amb un increment de vendes o assolint un major marge”
I pel que fa a la manera de treballar, quins aprenentatges heu fet?
En aquest sentit tenim molt clar que l’equip per abordar la fabricació additiva ha de ser multidisciplinari i transversal a tots els departaments. Per exemple, el departament de planificació de producció ha d’incorporar el nous terminis d’entrega, l’equip comercial ha de poder explicar al client que substituïm una peça de tota la vida per una de nova que no altera la qualitat final, etc. Això és molt important i no n’hem après fins la segona iteració que vam treballar. També considerem que aquest és un projecte que s’ha de gestionar amb mentalitat agile.
Continuareu fent servir la tecnologia de fabricació additiva?
Entenem que, en el nostre cas, aquesta tecnologia té molt més a veure amb el client que no pas amb les operacions. No només per l’estalvi de costos i la reducció de temps sinó per totes les potencialitats que la impressió 3D proporciona de cara a aportar més valor al nostre client. I d’això no en sabem prou encara, sobretot perquè no entenem encara totes les potencialitats que permet aquesta tecnologia. Per això tenim claríssim que això no ha fet més que començar i que la fabricació additiva serà un dels motors de transformació de l’empresa.