Mespack es un fabricante de soluciones de envasado flexible y final de línea, por lo cual diseña y produce maquinaria para empresas de bienes de consumo envasados en todo el mundo. Nacida hace 30 años como una empresa familiar, hoy en día forma parte del grupo Duravant y es una compañía innovadora que ofrece tecnologías creativas, funcionales y sostenibles de envasado. Precisamente por este espíritu innovador, identificó la oportunidad de incorporar la tecnología de fabricación aditiva para diferenciarse y ofrecer más valor añadido a sus clientes. Hemos hablado con Guillem Clofent, director general a Mespack, para que nos explique cuál ha sido su experiencia en la aceleradora y qué aprendizajes han extraído.
¿A qué os dedicáis en Mespack?
Somos una empresa líder en el sector de las máquinas para producir envases flexibles y finales de línea. Estas líneas de producción que fabricamos pueden llegar a tener 25 metros de longitud, y tenemos para el envasado de producto líquido, polvo y sólido, en formatos de sobre, doypacks (sobres que se aguantan de pie) y stick packs (los sobres alargados de azúcar, por ejemplo). También fabricamos unas máquinas que sirven para envasar productos en los que el material del envase desaparece con el uso del producto. Por ejemplo, pastillas hidrosolubles para lavavajillas y lavadoras o incluso productos con envase comestible.
¿Cómo llegáis a considerar el uso de fabricación aditiva?
Nosotros trabajamos e implementamos planes estratégicos periódicos. Justamente en el plan que acaba este 2023, hay algunas líneas que convergen de manera muy natural con la impresión 3D. Es lo que hemos llamado las 6R, y que nos hace trabajar para ayudar a la industria del envase flexible a adoptar lógicas de economía circular. En este sentido, la fabricación aditiva puede ayudar en la reducción, no solo de la huella ecológica, sino también en la mejora de las prestaciones y del valor que puedes ofrecer a los clientes.
“Trabajamos para ayudar a la industria del packaging flexible a adoptar lógicas de economía circular”
¿Cómo abordasteis la posible introducción de la impresión 3D en la organización?
Primero, de la mano de ThinkIn 3D nos planteamos una serie de objetivos a conseguir con la implementación de la fabricación aditiva. Desde conseguir una reducción de costes en la producción, pasando por mejorar la funcionalidad y prestaciones de lo que fabricamos, reducir los plazos de entrega y mejorar el nivel de servicio que ofrecemos a los clientes. Finalmente, también incluimos un objetivo que hemos llegado a comprender gracias a trabajar de la mano de la aceleradora, y es que esta iniciativa nos ayuda a promocionar y mantener el talento.
“De la mano de ThinkIn 3D nos planteamos una serie de objetivos a conseguir con la implementación de la fabricación aditiva”
¿Cómo se han concretado estos objetivos?
Uno de los productos que hemos hecho realidad incorporando la impresión 3D es la fabricación de un tubo muy sencillo que nos sirve para recoger el sobrante que generan las máquinas. Hasta ahora, fabricábamos esta pieza a partir de 3 sub piezas que, además, se tenían que soldar y llevar a pintar. Esto sin contar con que cada máquina que fabricamos tenía esta pieza, pero adaptada y, por lo tanto, hacíamos muchas piezas ligeramente diferentes que cumplían la misma función en maquinaria distinta. En esta situación era imposible aplicar economías de escala. Colaborando con la aceleradora hemos rediseñado esta pieza mediante fabricación aditiva y hemos logrado algunos de los objetivos de nuestra lista.
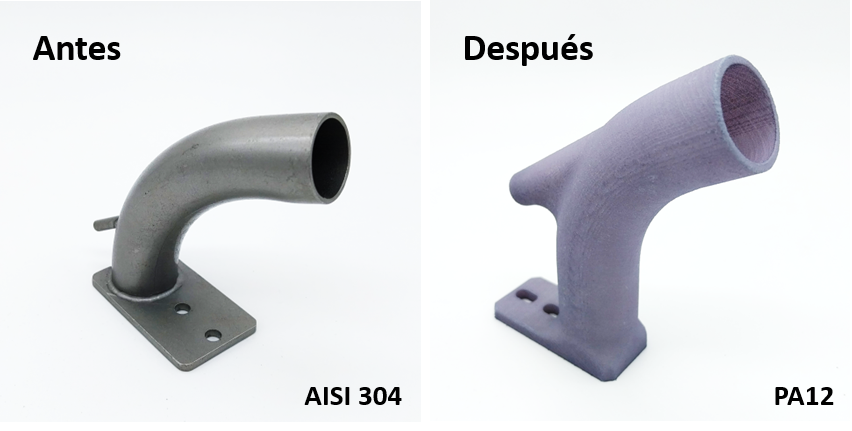
¿Qué objetivos habéis conseguido?
El más claro es una reducción del 45% del coste de fabricación. Pero también el hecho de que hemos podido estandarizar el diseño de la pieza para toda la gama de máquinas, de manera que hoy somos capaces de fabricar una única pieza que aplicaremos a toda nuestra maquinaria. Por otro lado, también hemos reducido el tiempo de entrega de la pieza de tres semanas a una semana o menos.
“Hemos rediseñado una pieza con fabricación aditiva y hemos conseguido una reducción del 45% del coste de fabricación”
¿Habéis llevado a cabo alguno otro desafío de impresión 3D con ThinkIn 3D?
Sí. También nos planteamos diseñar con fabricación aditiva un filtro que usamos para dosificar jabón. El reto de partida es que, cuando trabajas con jabón, debes vigilar de no aplicar mucha presión porque si no generas más espuma que líquido dentro del sobre. Pero, por el contrario, también nos interesa aplicar cierta presión para que el tiempo necesario para llenar el sobre sea lo más corto posible. Para solucionar este reto, fabricamos un filtro con perforaciones capilares que evitan la generación de micro espuma. Producir esta pieza hoy en día nos supone un coste muy elevado porque es de acero inoxidable y necesita de muchas horas de mecanización.
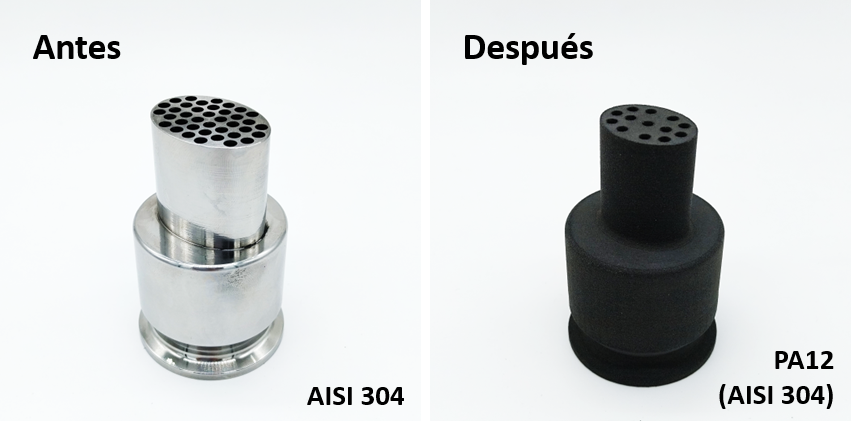
¿Cuál ha sido el resultado de abordar este reto con impresión 3D?
Hemos rediseñando la pieza y hemos podido reducir un 75% el coste de producción. Otra de las ventajas que hemos conseguido es una especialización en el diseño -filtros diferentes en función del producto a dosificar- con un tiempo de producción realmente rápido. Y, finalmente, hemos conseguido que el filtro diseñado reduzca el tiempo de dosificado y aumente la capacidad productiva del cliente.
“Otras ventajas que hemos conseguido es una especialización en el diseño y un tiempo de producción realmente rápido gracias a la impresión 3D”
¿Qué otros retos futuros os planteáis?
Actualmente este filtro es de poliamida, pero el objetivo es acabar fabricándolo de acero inoxidable para poderlo usar en aplicaciones alimentarias como, por ejemplo, los lácteos.
¿Qué lecciones habéis aprendido de este proceso de aplicación de la impresión 3D?
En primer lugar, a pesar de todos los ahorros en el coste de producción, estos márgenes no justifican la inversión que hemos hecho desde el punto de vista de la incorporación de maquinaria, la incorporación de equipo y su formación. Pero entendemos que lo más importante es que nos permite aportar mayor valor a nuestro cliente, y nosotros podemos capturar parte de este valor de diferentes maneras: logrando un mayor margen, por ejemplo, pero también con un incremento de ventas al ser capaces de ofrecer piezas de repuesto compitiendo con fabricantes locales porque precisamente podemos tener la pieza mucho más rápido que cualquier otra empresa local que fabrique por extracción.
“Hemos aprendido que la fabricación aditiva nos permite aportar más valor a nuestro cliente, y nosotros podemos capturar parte de este valor con un incremento de ventas o logrando un mayor margen”
Y en cuanto a la manera de trabajar, ¿qué aprendizajes habéis hecho?
En este sentido tenemos muy claro que el equipo para abordar la fabricación aditiva debe ser multidisciplinar y transversal a todos los departamentos. Por ejemplo, el departamento de planificación de producción debe incorporar los nuevos plazos de entrega, el equipo comercial ha de poder explicar al cliente que sustituimos una pieza de toda la vida por una nueva que no altera la calidad final, etc. Esto es muy importante y no lo hemos aprendido hasta la segunda iteración que trabajamos. También consideramos que este es un proyecto que se debe gestionar con mentalidad agile.
¿Continuaréis usando la tecnología de fabricación aditiva?
Entendemos que, en nuestro caso, esta tecnología tiene mucho más que ver con el cliente que no con las operaciones. No solo por el ahorro de costes y la reducción de tiempo sino por todas las potencialidades que la impresión 3D proporciona de cara a aportar más valor a nuestro cliente. Y de esto no sabemos bastante todavía, sobre todo porque aún no entendemos todas las posibilidades que permite esta tecnología. Por eso tenemos clarísimo que esto no ha hecho más que empezar, y que la fabricación aditiva será uno de los motores de transformación de la empresa.