In this day and age there are different industrial manufacturing technologies, each of which has specificities that make it more suitable for specific applications. Additive manufacturing is one more, but not the only one, and it is worth understanding them all to be able to have a global view.
In first place, subtractive manufacturing needs to be discussed. In these cases, the source is a block of material larger than the final geometry that you want to achieve. So, material is removed, selectively removing it, gradually creating the desired piece. Machining, electroerosion or cutting are examples of subtractive manufacturing.
In the case of conformal manufacturing, a matrix with the shape of the final geometry is used, in which material is introduced that gradually adapts to this shape. Some examples are injection moulding, forging or stamping, thermoforming or powder metallurgy.
Finally we have additive manufacturing, where the piece is created directly, adding material layer by layer. FDM, SLA or SLS are sub-technologies of 3D printing.
A closer look to additive manufacturing
Although for some people 3D printing may seem like a total solution for industrial manufacturing, in reality, like any other technology, it has advantages and disadvantages compared to other traditional processes. Let’s start by looking at the advantges.
3D printing advantages:
- Freedom in the design of complex pieces: One of its main virtues is that it allows you to create pieces with great design freedom, which is not possible with other manufacturing technologies. This autonomy is possible because the 3D printer adds material layer by layer, so geometries can be created with few limitations. In addition, additive manufacturing is also a very interesting option for companies and professionals who need to create personalized pieces or adapted to their specific needs because the manufacturing process does not involve an increase in the price of the final product.
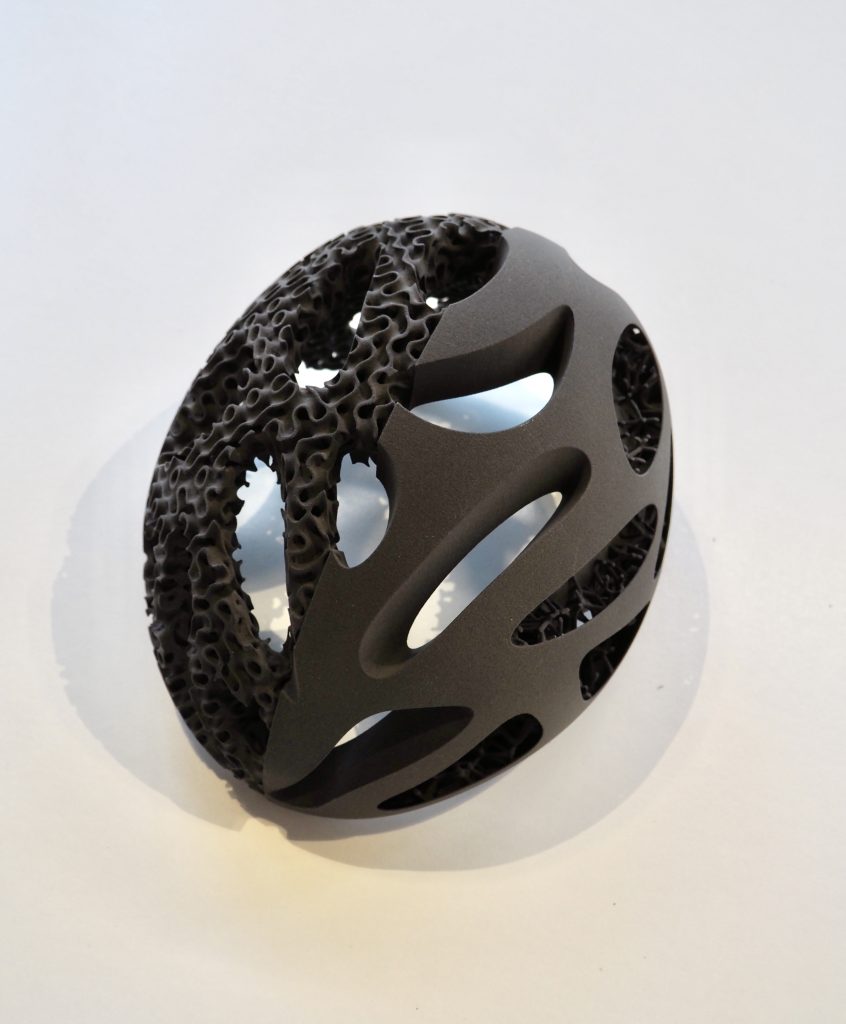
- Functions integration: Additive manufacturing makes it possible to create a single piece that integrates different functions or components instead of creating different parts that must then be assembled. This way you can get lighter parts that require less time to make and also there are advantages in terms of resistance and durability, since the assembling of parts can be a weak point
- Customization: The customization of pieces takes on a new dimension with 3D printing. This technology not only allows you to create unique pieces fully adapted to very specific sizes and needs. It is also possible to create pieces with specific functionalities or to design pieces with unique textures that are realized through the process of layer-by-layer material deposition. Imagine the possibilities that this technology opens up in sectors such as interior design or fashion
- Lighter products: Two design techniques that come into play in additive manufacturing make it possible to create pieces with less weight. On the one hand, thanks to topological optimization, it is possible to maximize the performance and effectiveness of the design by removing material from areas that do not need to support large mechanical loads. This design process is obtained from finite element calculations (FEM) under initial conditions given by the designer. On the other hand, thanks to the generative design, the program generates the final shape of the part according to the same conditions given in the topological optimization but without prior material to extract, but instead generates the “minimum paths” of material necessary to support the loads within a predetermined volume. Thanks to these two design techniques, it is possible to reduce the weight of the parts and, at the same time, increase their resistance and durability.
- Multi-material products: Some 3D printing technologies can simultaneously apply several materials during the manufacturing process. This allows, for example, to reinforce the mechanical properties of the final piece by applying carbon fiber to the same impression, or to include different colors or hardnesses to be able to create a surgical model.
- Fast set-up: With subtractive technologies you generally have to create molds or set up heavy production machines, and this has an impact on the time that lengthens the manufacturing cycle. Instead, a 3d printer, can be installed easily – depending on the technology, of course-. In addition, we can obtain one or several pieces in a matter of hours without the need to own special tools.
- Cost and Bug reduction: This technology offers us to create products from a single piece avoiding assemblies, the possibility of making mistakes during the production process is also limited. In terms of costs, the fact of being able to create tailor-made tools and only use them when necessary can also reduce intermediate costs and/or processes, such as the need to have an industrial warehouse to store all these elements that are only used in one production.
- New designs time-to-market reduction : The use of 3D printing in prototypes manufacturing has made it possible to accelerate the launch into the market of several products due to the speed with which the manufacture is approached between iterations. In this scene, the following logical step is the adoption of additive manufacturing as a final product manufacturing technology. Currently, however, we already find some cases where the final piece is being produced with 3D printing: mouth guards or dental models for thermoforming in the dental field, custom glasses, custom foot insoles or shoe soles.
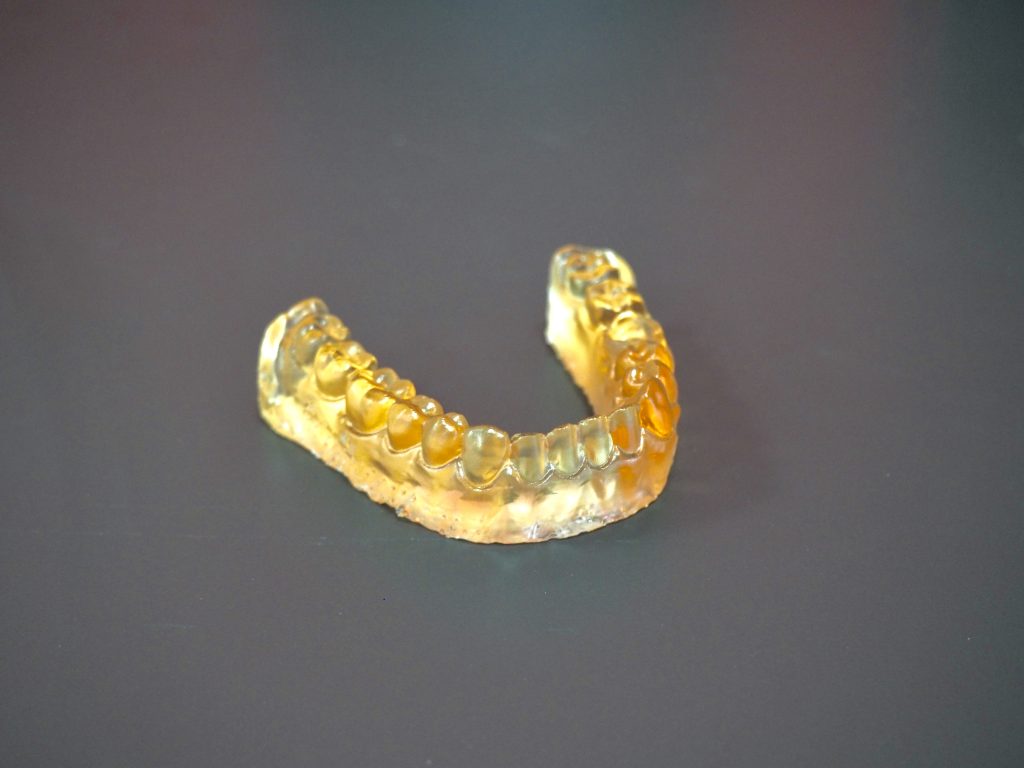
As we said, although 3D printing is being revolutionary in many aspects, like all emerging technology, it also has some drawbacks. It’s time to explore some of the most common problems with this technology.
3D printing disadvantages:
- Unsuitable for large production series: The investment in injection molds is amortized in the manufacture of large volumes of pieces. In contrast, the unit cost per piece with additive manufacturing always remains the same.
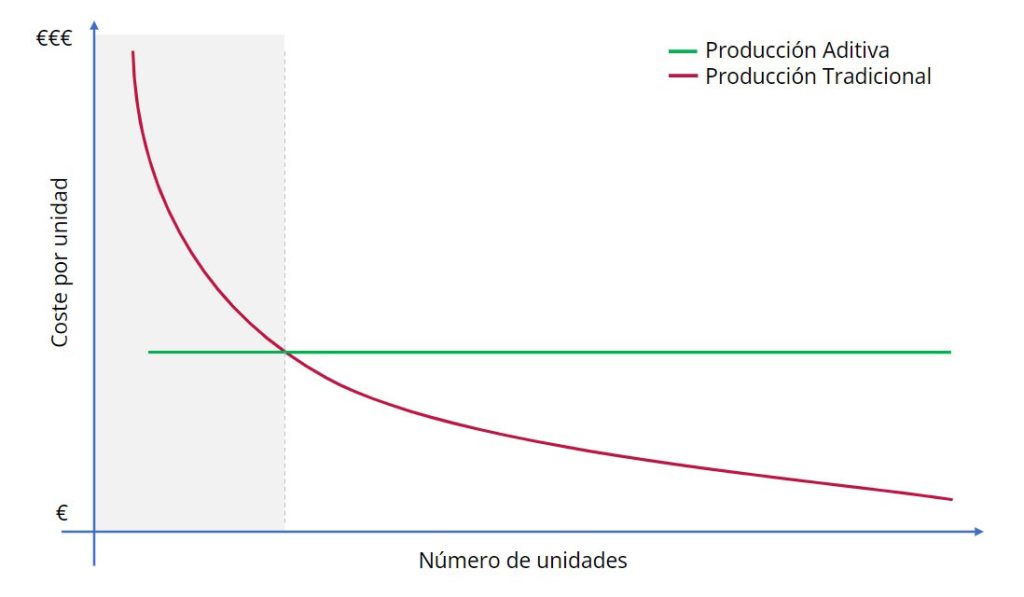
- Little variety of production materials: The range of material options that this technology has in both metals and other materials is great, but it is not comparable to what can be done with substative and conformative manufacturing. Considering, moreover, that the cost of these materials is usually higher in additive manufacturing.
- Surface finish of the pieces and manufacturing speed: The layer-by-layer manufacturing process ends up affecting the surface aesthetics of the piece. The solution, which would be to reduce the thickness of the layer, directly affects the total manufacturing time, extending it. Comparatively, then, the manufacturing time is slow compared to subtractive methods.
- Product quality and process repeatability: 3D printing cannot always ensure reliability in process repeatability. What does it mean? That the pieces do not always have the same quality. This problem has an impact on the physical properties of the parts (elasticity or hardness, for example) and this makes it difficult to obtain production certification in areas such as the medical or aeronautical sectors.
- Pieces’ size limitation The volume of the final piece will be linked to the printing volume. This means we are limited by the size of the 3D printer.
- Equipment cost and productivity: Currently the cost of industrial 3D printing machines is high, and this affects the price of the final piece. As always happens with any new technology, the forecast is that this cost will be reduced as the application of each additive manufacturing technology becomes more widespread.
When will we use subtractive or additive manufacturing?
Generally speaking, manufacturers tend to use 3D printed pieces to create custom products, with low production volume, or to manufacture out-of-stock parts. Instead, they opt for subtractive processes in metal when creating high production volumes or parts that require other mechanical properties.
However, both subtractive and additive manufacturing can be used in parallel and at different stages of product development and manufacturing to take advantage of the advantages of each process. For example, in the manufacture of prototypes the two types of manufacture are combined. Using both processes in parallel, a more complex final part can be created with better mechanical properties
First prototypes, whether only volumetric or functional, tend to be cheaper and faster to produce with 3D printing technologies such as SLA, SLS or FDM. They can also be combined with CNC produced metal parts.
Some specific examples in which both technologies can be used in a complementary way are the tooling production, fastening and fixing devices, supports, molds and stamping patterns.